Italian 3D printing company WASP has joined forces with Mario Cucinella Architects to construct an innovative 3D-printed dwelling. Dubbed TECLA, the first prototype is undergoing construction and is located just outside of Bologna, Italy. We've been following the work of WASP for some time and have previously reported on its Big Delta and clay and straw shelter projects. However, the TECLA prototype is an exciting new project for the company, involving the creation of a circular eco-housing model, built using one hundred percent reusable and recyclable materials.
“The design inspiration for TECLA comes from our desire to achieve two key things: a self-supporting structure, which takes advantage of 3D technologies and local terrain to produce a fully functioning house without the risk of collapsing; and a modular house, which is easy to assemble in different configurations according to specific local conditions and needs,” Mario Cucinella Architects tells New Atlas.
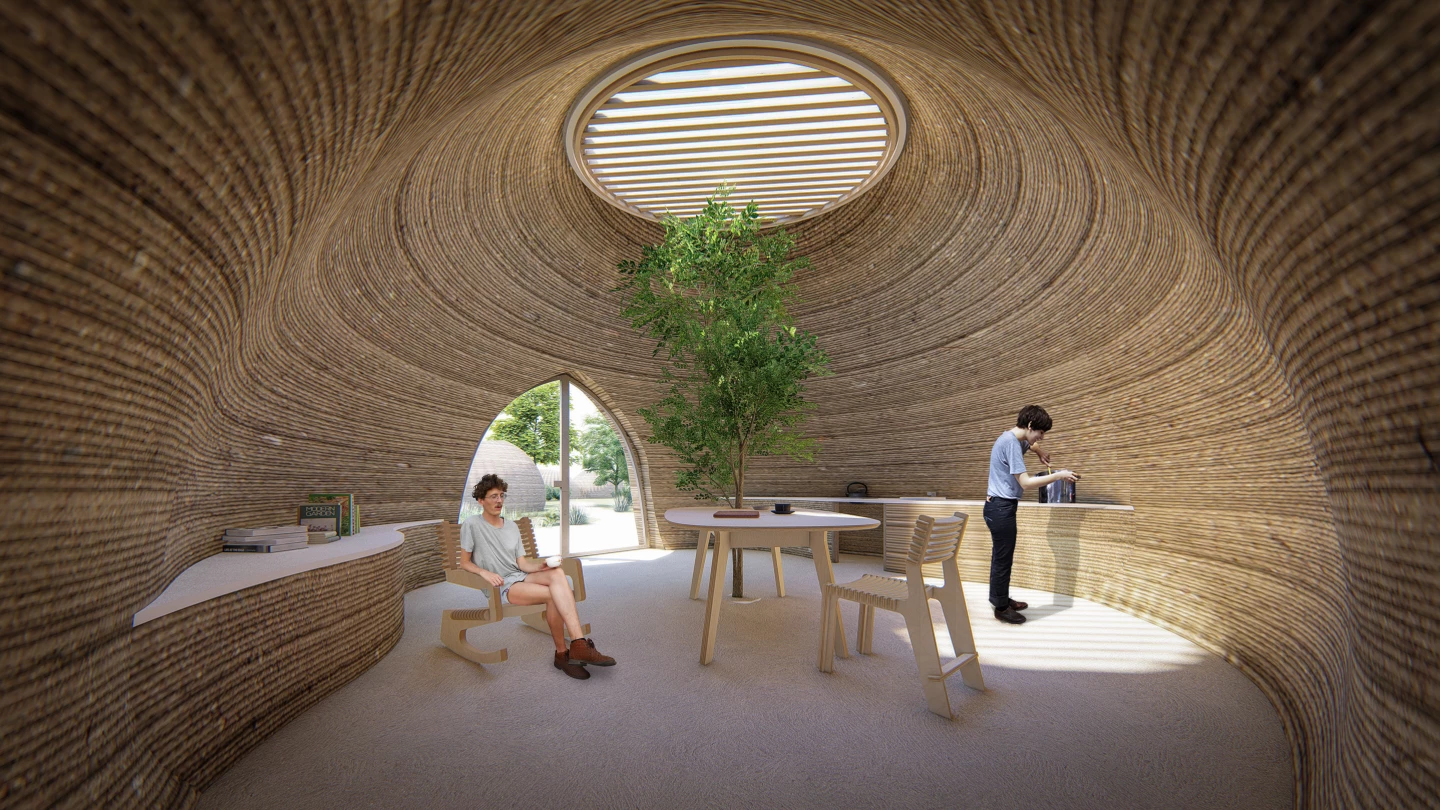
The overall design incorporates thermo-insulation, ventilation and water collection within a single structure. While the unique dome shape of the dwelling is an effective way to enclose the building without the need for support structures during the construction process. Furthermore, the design has been developed to be easily adaptable to print in different locations and climate conditions.
The first TECLA prototype will consist of two basic modules with a total area of 55 sq m (592 sq ft), and a maximum height of 4 m (13 ft). The construction process involves a digging and a mixing phase, where local terrain is mixed with water and additives, before construction starts. Engineers first analyze the soil samples before proceeding with printing the external structure of the house. This printing phase involves collecting the clay mixture and funneling it into different forms, layer after layer, until the desired shape is achieved.
“The construction process is certainly the main challenge of TECLA,” WASP CEO Massimo Moretti tells New Atlas. “3D printing through natural mixtures allows us to achieve a high range of thermal insulation, as well as minimum environmental impact.”
“Once the printing process is complete, it usually takes some time for the layers of clay to dry, this is an element that is normally affected by external factors, such as humidity and local weather conditions,” adds Mario Cucinella Architects.
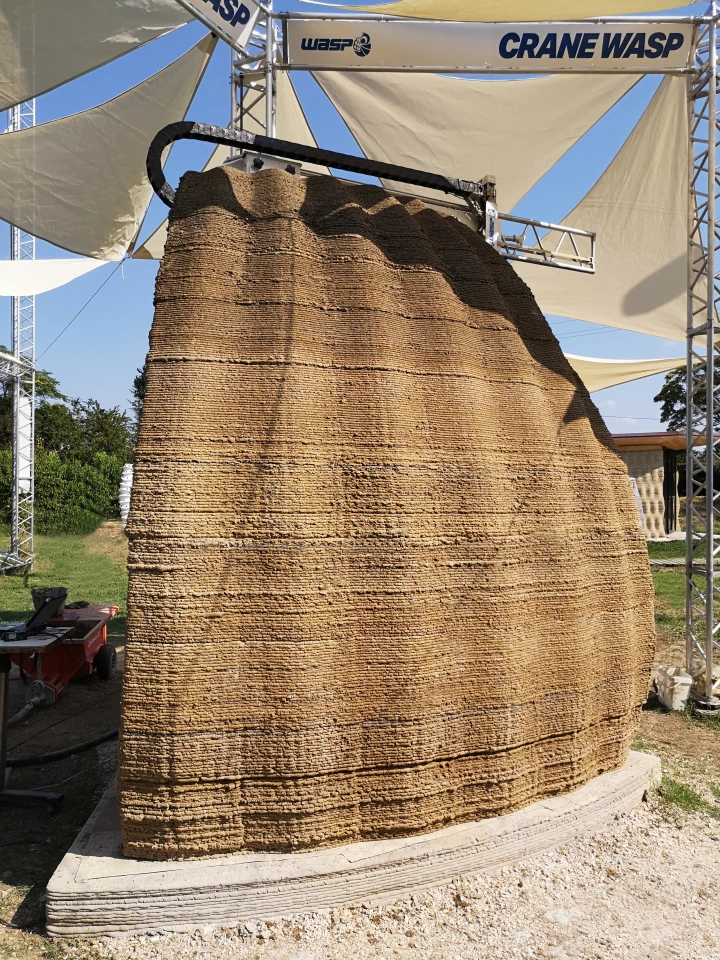
Each TECLA house features a living room, bedroom, bathroom, entrance door and skylight. The interior finishings and furniture will be specially customized for the project, including key features made with 3D printing and locally sourced timber; such as the bed and kitchen counter. The dwellings are conceived to be very open and flexible, however as the prototype does not feature any windows, it will be possible to add these later on in the process and according to the home's final use.
“Although the overall design might seem quite simple, the internal infill, which is never visible, and the external skin pattern have both been developed following the latest studies in the field of environmental design: solar radiation has helped define folds on the external envelope, which are quite pronounced in areas that are more exposed to sunlight, while thermal simulations have helped us determine parameters of the infill,” says Mario Cucinella Architects. “These findings have allowed us to overcome challenges in traditional building methods. The real innovation behind TECLA lies in the external envelope as well as in the choice of natural and locally sourced materials.”
At this stage the teams are unable to define a clear public cost for the housing models, as it depends on the scale of production. However, the 3D printing technology does allow them to achieve a cost effective and sustainable solution compared to traditional building methods. In addition the 3D printing technology will allow them to print a house the size of TECLA in just two weeks.

“We are optimizing the construction rate, developing the most efficient way to use simultaneously two Crane WASP printers,” says Moretti.
TECLA was given planning permission in May this year, printing started in September and it is scheduled for completion at the beginning of March 2020. The final building will be used as a functional case-study for an off-grid housing model. It will be available for daily events, in order to test out living inside the clay habitat.
Once the TECLA project is complete WASP and Mario Cucinella Architects intend to build a smart village of 3D-printed houses.
Sources: WASP, Mario Cucinella Architects